Carbon fiber has the potential to change industries around the world. Lighter cars, compressed gas storage and stiffer, more efficient wind turbines are examples of its many uses.
In the past, large-scale use of the product was stifled by cost and volume limitations. Not anymore.
Thanks to a recent breakthrough at the Oak Ridge National Laboratory (ORNL), scientists have discovered how to produce the carbon using a low-cost input material — the same acrylic fiber found in carpets, socks and shirts — instead of carefully processed, more expensive specialty fiber.
The carbon is produced through a high-temperature process that converts acrylic fiber, stripping away material other than carbon. The new, low-cost process allows the carbon fiber, a strong material used for reinforcement in advanced composites, to be affordable for use in the automobile industry.
“The innovation is the use of a material that is really designed for commodity products in the same way we use specialty fiber that is more carefully processed and therefore much more expensive,” said Alan Liby, deputy director of the Advanced Manufacturing Program at Oak Ridge National Laboratory. “That is part of the cost reduction, simply using a low-cost input material.”
Combined with a new capability to processing larger quantities per batch, the innovation will drastically cut the cost of carbon fiber, which previously sold for $10 per pound. Processing higher quantities of lower-cost material will reduce the price of the product by more than 50 percent, according to Liby.
The energy used to produce it will be lessened by around 60 percent, a boost for the environment.
The cost reduction will support carbon use in lightweight components for vehicles, which is the biggest target use, according to Liby. Gas storage vessels made from the fiber will hold a higher pressure, and therefore store more gas in a higher volume, important for eventual use in hydrogen-fueled and over-the-road vehicles.
“It can dramatically increase the use of carbon fiber-reinforced composites to replace heavier materials like steel, aluminum and fiberglass-reinforced composites,” Liby said. “All of those materials weigh more for a given purpose than carbon fiber-reinforced composite materials.”
The weight of a car potentially could be lessened to meet the fuel economy standards set for the future, according to Liby, who said meeting the government’s 54 miles-per-gallon target for light-duty vehicle fuel efficiency by 2025 is a huge challenge.
“The drive for energy efficiency is an important one to support what’s being referred to as the ‘clean energy economy,’ ” Liby said. “The entire world is engaged in this process, but competitively we don’t want to fall behind by not being on the forefront of this kind of technology.”
The carbon fiber industry is a portion of the focus of the Institute for Advanced Composites Manufacturing Innovation, or IACMI-The Composites Institute, a White House-initiated public-private partnership between universities, governments and laboratories.
The group is working to benefit the country’s energy security through resource and investment sharing, with the goal of developing advanced composites. The partnership also has a heavy hand in training the workforce to meet employment opportunities that the field is quickly generating.
IACMI has an East Tennessee foundation. The national partnership is headquartered in Knoxville and has strong ties to Oak Ridge National Laboratory and the University of Tennessee.
“What we’re doing inside The Composites Institute is getting after energy reductions which ultimately will lead to cost reductions, and moving towards high-volume manufacturing with the automotive, compressed gas storage and wind,” IACMI CEO Dr. Craig Blue said.
Read the full article IACMI article.
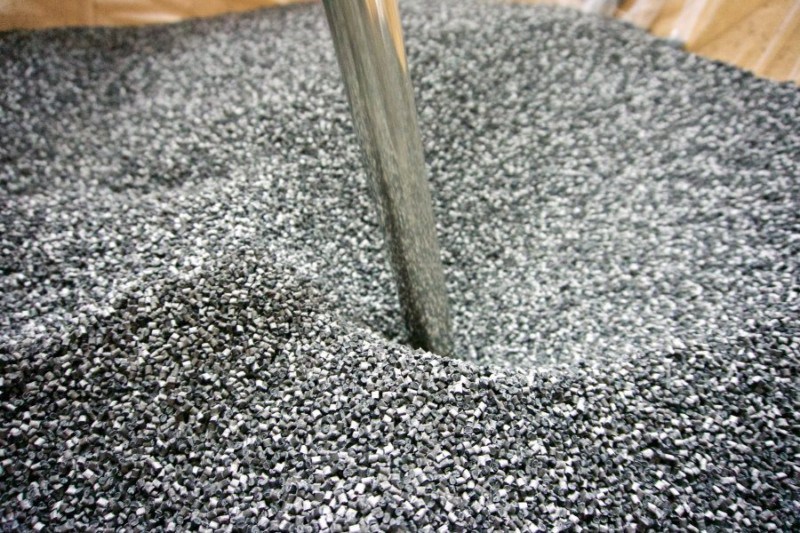