“Remember Goldilocks—not too fast, not too slow, just right. You ready?” That’s Dr. Bob Voigt, a Materials Science and Engineering professor at Penn State University, coaching me on my first casting experience.
I’m wearing a reflective silver suit from head to toe, high-temperature gloves, and a face shield. Minutes before, I’d been scooping sand around polystyrene, lifting the flask with an overhead crane, and peering into molten Aluminum 356 that looks like mercury that escaped from a giant thermometer. As Bob tilts the induction furnace, I catch a stream of liquid metal in the ladle.
In a process called lost foam casting, the metal instantly vaporizes the Styrofoam mold and fills in the impression for a custom stein. Ten seconds is all it takes.
This is the world of casting, an industry that walks the line between traditional art and modern science.
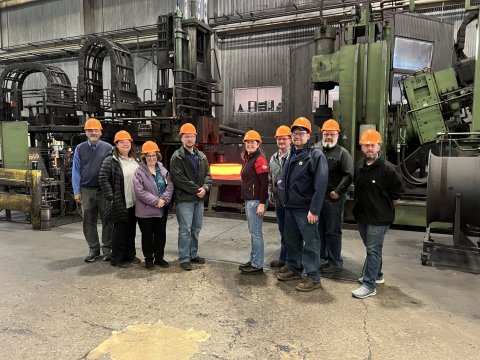
Casting and Forging 101
My career up until now as a television producer gave me some pretty cool opportunities, including working with Mike Rowe in the precursor to Dirty Jobs, but I’ll get back to that. If someone gives me the chance to try something new—especially if it scares me a little—I jump right in. Now that IACMI is working on a new workforce initiative called METAL (Metallurgical Engineering Trades Apprenticeship & Learning), I’m pushing aside my fears of spilling thousand-degree metal to understand why this is a career worth pursuing.
For five days, I’m traveling from one end of Pennsylvania to the other, trying to get beyond what I’ve gleaned about casting and forging (C&F) from pop culture. I’m getting a diverse taste–from companies that produce critical assets for the U.S. Department of Defense (DoD) to school foundries giving hands-on training.
So, here’s a brief overview of C&F from the novice perspective. In casting, you heat metal to melting and then pour it into the shape you want, like melted chocolate into heart-shaped molds. In forging, you heat metal until it’s soft enough to change its shape with pressure. Most of us picture the blacksmith pounding a piece of steel with a hammer. Forges today have much, much bigger tools.