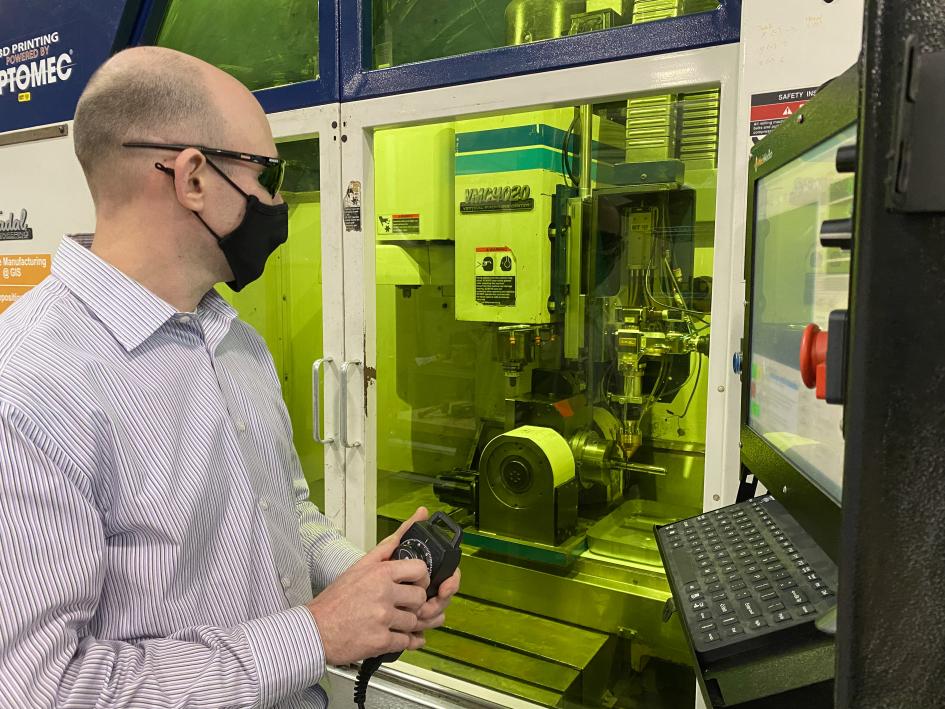
The industrial sector is the backbone of America’s economy. And to manufacture the products that society relies on, industry consumes 33% of the nation’s energy and accounts for 29% of America’s carbon emissions. Reducing emissions across the industrial sector is a key component of the Biden Administration’s set of economy-wide goals to create an equitable clean energy future. From capturing lost heat discharged into the atmosphere to adopting a circular economy approach to manufacturing, improving industrial energy efficiency will help us achieve these goals.
Reducing energy consumption and using energy as efficiently as possible are crucial for U.S. manufacturers to not only reduce emissions and confront the climate crisis but to also create jobs for current and next generation workers and increase America’s global competitiveness in the industrial sector.
Manufacturing USA is a network of 16 institutes and their sponsoring federal agencies — the Departments of Commerce, Defense and Energy – that was created to secure U.S. global leadership in advanced manufacturing through large-scale public-private collaboration on technology, supply chain, and education and workforce development.
The network is responding to the need for increased energy efficiency and reductions in carbon emissions by fostering projects that will lead to major reductions in manufacturing energy use and costs, and provide the basis for innovative new green products.
Given that future energy consumption is likely to increase, cost-effective power conversion in industrial applications will prove vital to save energy and lower expenses for industry, reduce emissions, industrial waste, materials and water usage, and improve the life cycle energy efficiency of manufactured goods.
Data Center Usage Shows Opportunity to Reduce Cost, Maximize Innovation
Tech companies such as Facebook, Amazon, and Google run massive cloud computing data centers. As we all store and process more information in the cloud, the demands on our wired and wireless networks multiply. Data centers now use about 2 percent of electricity consumed in the U.S.
Data centers represent a huge challenge for power and efficiency. They also represent how the Manufacturing USA network is bringing an innovative approach to developing energy efficient technologies. AIM Photonics’ work in silicon integrated photonics has helped position the U.S. as a leader in this groundbreaking technology.
Integrated photonics, or photonic integrated circuits (PICs), are similar to their electronic counterparts but use light instead of electrons. Moving data with photons (light) is more efficient than using copper wire and electronics, therefore many of the bottlenecks in energy, heating, and processing speeds are alleviated. AIM Photonics’ advanced manufacturing of silicon photonics can closely integrate key photonic devices: modulators, lasers, detectors, and waveguides, along with the predominant technology for manufacturing integrated circuits. It unlocks the power of light on a silicon chip.
Using integrated photonics, data centers will be able to handle greater scale of data with nanosecond switching speeds, while consuming only half as much power, resulting in a dramatic cost savings.
How Institutes Are Addressing Energy Consumption and Efficiency
Many institutes in the Manufacturing USA network are working with research entities and private sector companies on multiple projects related to power conservation and energy efficiency. Here is a look at some of the many initiatives:
PowerAmerica: Accelerating Commercialization of Clean Energy in Semiconductors
PowerAmerica is an institute whose mission is accelerating the commercialization of silicon carbide (SiC) and gallium nitrate (GaN) wide bandgap semiconductor power electronics. It has stood up a vibrant U.S. silicon carbide fabrication infrastructure that mirrors that of silicon. SiC and GaN are more efficient materials for power conversion systems, but are more expensive to produce than standard silicon devices widely used in power electronics systems. The institute has worked with several semiconductor producers to develop processes that reduce the production cost of the devices. They have also collaborated with companies in the EV charging and traction, solar energy, consumer electronics, electric grid, data center, and industrial motor sectors to demonstrate the superior energy efficiency of SiC and GaN in these energy intensive applications.
MxD: Future Factory Helps Manufacturers Make Every Part Better
MxD, Manufacturing times Digital, has built a cutting-edge factory of the future with examples of how technology can help manufacturers reduce costs and use power more efficiently. For instance, MxD shows how low-cost sensors can monitor legacy machines’ activity to determine whether they are on or off. This can inform decisions about machine utilization and manufacturers can begin using their equipment more efficiently based on this data.
CESMII: Integrating Sensors, Controls and Data to Increase Energy Productivity
CESMII, the Smart Manufacturing Institute, has integrated sensing, control, analytics and predictive modeling into an environment where they can exchange information in a seamless manner to optimize operations and reduce energy consumption. One CESMII project used a predictive model to realize a 15 percent reduction in energy usage in production kilns for cement manufacturing, an extremely energy-intensive sector.
RAPID: Improving Energy Efficiency in Chemical Processing
RAPID is dedicated to boosting energy productivity and energy efficiency through manufacturing that involves chemical processing. One project is focused on the separation of olefins and paraffins – a foundational process step that produces chemicals such as propylene and ethylene, the building blocks for numerous petrochemicals. Currently this process uses distillation, an energy-intensive process that by itself is estimated to consume 0.3% of the world’s energy. RAPID’s project is testing the use of a polymeric membrane to recover propylene from propane in a polymerization reactor purge stream, which would normally be simply burned and thus wasted. This process recycles 90% of the propylene that would normally be lost, resulting in a reduction in energy consumption. The goal is to demonstrate the potential for membrane separation technology by applying it to one part of the olefin-paraffin separation process. Ultimately the shift to membrane separation technologies throughout the process has the potential, according to one analysis, to reduce energy consumption by up to 80%.
REMADE: Transition To A Circular Economy
REMADE is dedicated to accelerating the U.S.’s transition from a “take-make-dispose” linear economy to a “make-use-reuse-remanufacture-recycle” circular economy. The REMADE Institute (Reducing EMbodied-energy And Decreasing Emissions) develops innovative technologies to increase the reuse, remanufacturing, recovery and recycling of four energy-intensive materials: metals, plastics/polymers, fibers, and electronic waste. For example, the portfolio of films and flexible packaging recycling projects is capable of saving up to 50 petajoules of energy annually, up to 2 million metric tons of materials savings per year, and decreasing greenhouse gas emissions by up to 2 million metric tons annually.
IACMI: Composite Automotive Components
IACMI: The Institute for Advanced Composites Manufacturing, researched and demonstrated many energy efficient applications of composite materials which are used in wind energy, automotive, and other industries that value light weight and high performance. Examples include qualification by Ford and VW of new carbon fiber products and processes suited to the high-production rates needed in the automotive industry, and successful recycling projects such as reuse of carbon fibers in an injection molded fender by Vartega resulting in at least a 43% reduction of embodied energy of automotive components. This supports the institute’s goal of a 50% reduction in carbon fiber reinforced plastic’s embodied energy, and addresses industry’s sustainability concerns, thus enabling these lighter weight materials offering improved strength, fuel efficiency, and crashworthiness, to be considered for deployment at scale.
CYMANII: A Cyber Secure Energy ROI for Manufacturing and Supply Chains
CYMANII: The Cybersecurity Manufacturing Innovation Institute is developing a secure manufacturing architecture that enables manufacturers to realize energy efficiency gains (and other operational improvements) across automated manufacturing operations and manufacturing supply chains. CyManII is working with industry to demonstrate how cybersecurity implementation can result in a return on investment rather than simply another cost of manufacturing. CyManII also is on the path toward establishing expectations and standards for incorporating security in all phases of design and development that can be followed and trusted by original equipment manufacturers, small- and medium-sized manufacturers, operator training simulators and integrators to help them achieve secure energy savings.
LIFT: Strengthening Our Military’s Armored Vehicles
LIFT is working to develop and deploy advanced lightweight materials manufacturing technologies. They have supported the development of an iron-manganese-aluminum alloy for use as armor on military ground vehicles. The steel is expected to reduce armor weight by more than 10 percent while matching or exceeding the ballistic performance of rolled homogeneous armor. Through this project, LIFT is optimizing processing conditions to produce affordable, high-quality armor plate in large volumes that also costs less to operate.
NextFlex: Reinventing Power and Energy Storage Subsystems
NextFlex, America’s Flexible Hybrid Electronics Manufacturing Institute, is helping reinvent power and energy storage subsystems, including batteries, supercapacitors, wireless power, and energy harvesting approaches that come with flexible and often wearable electronic devices. The promise of flexible hybrid electronics includes not just flexibility but also less weight and expense as the industry expands beyond centralized processing units and expensive and heavy printed circuit boards.
America Makes: Integrating Technologies To Improve Manufacturing Efficiency
America Makes, which develops and expands capabilities in additive manufacturing and 3D printing, led a team to design and assemble a new Multi3D system, which reduced cost and space requirements on a shop floor by more than 50 percent. The system has a five-axis motion platform for additive manufacturing, subtractive manufacturing, and foil/wire embedding. The result is the capability to design and manufacture multifunctional components within a single enclosed unit, reducing the time and cost of end-to-end production.
Powering the Advanced Manufacturing Movement
The initiatives described above demonstrate how the institutes in the Manufacturing USA network are exploring ways to reduce energy consumption, meet the nation’s decarbonization goals, and develop a strong, resilient domestic manufacturing sector. These projects also illustrate the value of the large-scale collaboration and innovation that the institutes enable throughout the U.S. manufacturing sector.
In 2020, 16 manufacturing innovation institutes collectively worked with over 2,000 member organizations to collaborate on more than 500 major research and development projects and engaged over 70,000 people in building workforce knowledge and skills in advanced manufacturing. State, industry and federal funds contributed $400 million to these activities.
To learn more about innovative ways to reduce energy consumption, convert energy and produce energy-efficient power, visit the institutes’ page.