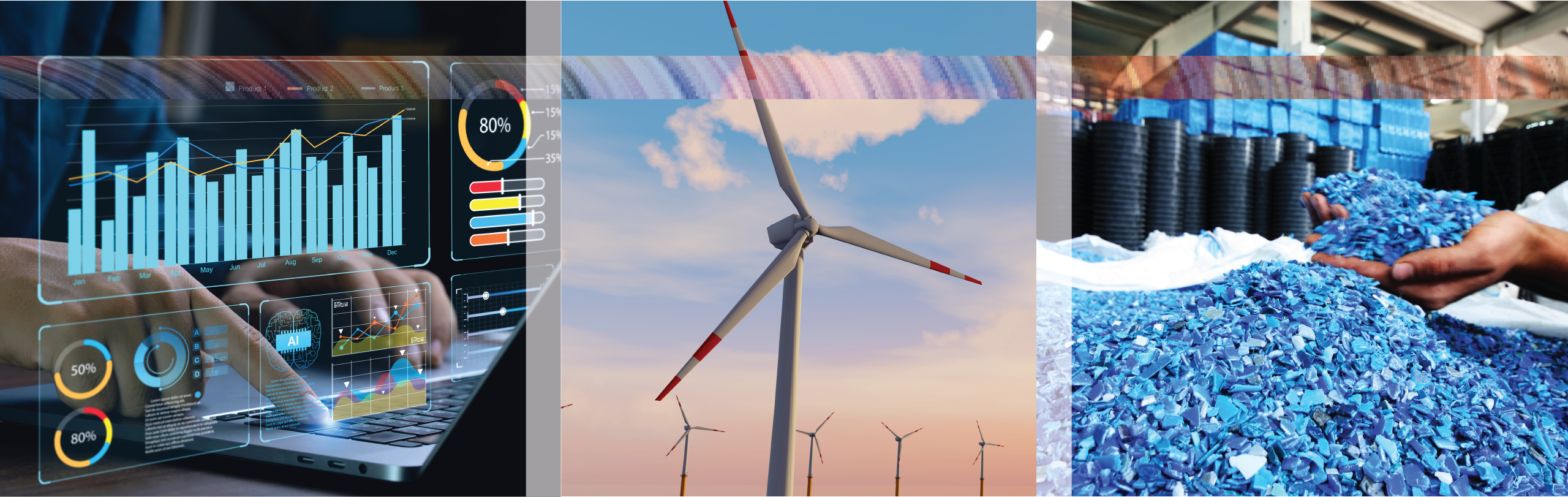
Reimagining Industrial Energy Use With Digital Technology
Today, manufacturing accounts for 25 percent of U.S. energy consumption and carbon emissions, and the industrial sector as a whole is the single largest contributor to greenhouse gas emissions in the nation, at 30 percent. Changing how industry produces materials and products is unquestionably critical to achieving our nation’s climate goals.
In close collaboration with industry and academia, the 17 manufacturing innovation institutes in the Manufacturing USA network are developing next-generation digital and other innovative technologies to reduce energy use and decrease emissions. The institutes are also working to deploy these capabilities in new ways to enhance sustainability as the industrial sector also confronts how to address its reliance on increasingly scarce resources.
Transitioning to clean energy plays a major role in achieving net-zero emissions by 2050 – one of the top climate goals set out in the United Nations’ Paris Agreement in 2015. But clean energy will only help reduce carbon emissions by 55 percent. To get all the way to net-zero, we need to change how we produce products and consume materials. Rather than throwing used products and materials away, we need to find ways to reuse, remanufacture, recover, and recycle them – a circular approach referred to as “Re-X.” The technology development and deployment underway at the manufacturing innovation institutes is critical to this transition.
The institutes are building collaborative innovation ecosystems that include research entities and member companies to dramatically reduce industrial energy use and emissions. Digital technology enables sensors and connected devices to collect real-time data from processes to enhance efficiency, productivity, and flexibility and identify ways to radically reduce energy use, eliminate waste, and recover and reuse materials.
REMADE Focuses on circular economy, minimizing waste, and maximizing resources
To tackle the remaining 45 percent of emissions, the REMADE Institute is focused on the Circular Economy, developing sustainable technologies that reduce energy use, decrease emissions, minimize waste, and maximize resources. By disseminating these technologies across supply chains, the REMADE Institute is accelerating the U.S.’s transition to a Circular Economy, where products are designed to last longer and can be reused, remanufactured, and recycled.
“Remanufacturing can reduce greenhouse gas emissions by between 80 and 98 percent and eliminate the need for new materials by 80 and 98 percent, depending on the application,” said Magdi Azer, REMADE’s Chief Technology Officer.
REMADE and its members are working to transition from the current “take, make, dispose” linear economy model, to a sustainable “make, use, reuse, remanufacture, recycle” Circular Economy approach. For that to happen, industry must fundamentally alter how it consumes materials, and designs and uses products.
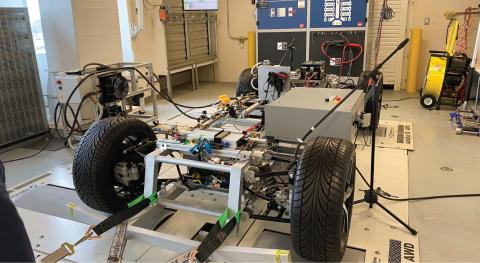
The use of aluminum is a good example of how digital technology can deliver these outcomes. Aluminum is widely used in the aerospace and automotive industries because it allows manufacturers to reduce weight, energy consumption, and emissions simultaneously. Unfortunately, it requires a significant amount of energy to produce aluminum. With global demand for aluminum expected to increase by 40 percent by 2030, and without the capability to produce new aluminum domestically, industry has increasingly tried using recycled aluminum, which requires 20 times less energy to produce than new aluminum. For some alloys, manufacturers must exclude or minimize the use of scrap. To reduce energy and emissions, one REMADE project team is utilizing smart sensors and artificial intelligence to control how much scrap material can be used.
REMADE is also working with its partners to convert ethyl-vinyl-acetate, or EVA foam, which is used in the midsoles of shoes, into material for new shoes. With more than 23 billion shoes produced globally every year, this project will allow shoemakers to use five times more used midsoles in the manufacturing of new shoes and sneakers. In return, this will reduce energy use, decrease emissions, minimize waste, and maximize materials.
Manufacturing Must Design for Reuse, Not Planned Obsolescence
A core principle of REMADE and the Circular Economy is to design products to increase reuse, remanufacturing, and recycling capabilities. Products often are designed for ease of assembly, with durability in mind. For example, cell phones have many glued parts which cannot be easily replaced.
“It will be a challenge to get design engineers and companies aligned on the importance of turning something that can’t be recycled into something that can,” Azer said.
Moreover, many industries, such as consumer electronics manufacturers, have engaged in “planned obsolescence,” designing products with a limited lifespan so that consumers would have to discard them for upgraded models or devices that are supported by new platforms. These practices have led to e-waste becoming the fastest-growing waste stream in the world, Azer shared. Globally, 50 million tons of e-waste is generated per year, and by 2030 that number is expected to grow to 75 million tons.
REMADE is working to tackle this critical issue with investments in numerous e-waste R&D projects, including those that will make the disassembly of smartphones easier and those that will increase the recovery of precious minerals from discarded electronics.
CESMII Provides an Entry Point to Smart Manufacturing
CESMII, the Smart Manufacturing Institute that was founded in 2016, learned quickly that energy efficiency by itself was a tough sell for manufacturers, especially the smaller, resource-challenged companies that make up the bulk of the sector. Manufacturers historically have focused on cost-effective operational efficiencies. However, digital technologies that improve production also reduce energy and eliminate waste.
Capturing real-time data is central to the adoption of Smart Manufacturing. Digital technologies can help manufacturers ensure that information is flowing to the right people for visibility, allowing them to more rapidly evaluate, control, and improve processes. In some cases, machines can make adjustments automatically based on real-time data.
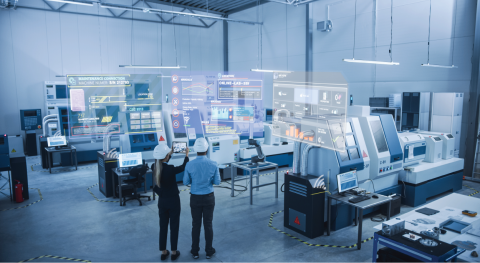
CESMII and its partners have established an entry point to Smart Manufacturing for small- and medium-sized manufacturers with low-cost sensors to enhance existing equipment as opposed to purchasing new equipment. The manufacturer gets access to data and can use the data to improve operational efficiencies. The clean energy benefits are tightly coupled with operational efficiency.
CESMII continues to develop ways to enhance advanced sensors, controls, platforms, and modeling. Their approach to Smart Manufacturing architecture creates the optimal environment for plug-and-play technology for all of industry – discrete, hybrid, and process. By leveraging data contextualization in the Smart Manufacturing Interoperability Platform (SMIP), data from operations can be broadly leveraged without being locked into a particular vendor. This work is vital for changing the paradigm to reduce energy consumption for all manufacturers.
IACMI Leverages Digital Technology to Advance the Use of Composites
While not all of the Manufacturing USA network institutes are dedicated to digital technology, they all rely on digital technology to advance their discipline. IACMI – The Composites Institute – is a good example. Digital technologies have transformed the composites industry through design and simulation, monitoring manufacturing processes for quality control, and integrating sensors to produce smart materials that can adapt to changing conditions.
One of the success stories in the IACMI ecosystem is developing a lighter-weight SUV liftgate using composite materials. Traditional composite approaches could only achieve a 20 percent reduction in weight. A digital twin simulation process allowed engineers to identify potential design flaws early in the development process. It also simulated the behavior of the product in a virtual environment. This helped avoid costly rework and redesign later in the prototyping stage. In this case, the stakeholders on the project were able to reduce assembled liftgate weight by 40 percent, which leads to less energy usage during operation, and reduces recurring part manufacturing cost by 9 percent versus steel stamping and welding.
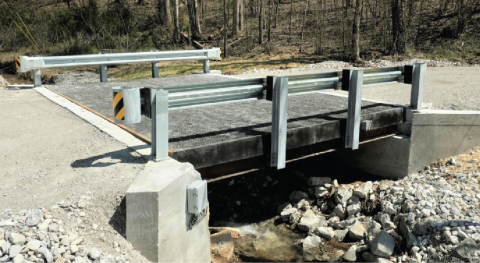
Another example is a small composite bridge installed on a quiet road in East Tennessee. The bridge deck is made of a fiber-reinforced polymer (FRP) and was installed in just two hours. It is projected to last 100 years, far longer than the traditional concrete bridge that weighs 10 times as much and would require replacing several times over the same period. It’s also a smart bridge, with embedded sensors to flag any issues and monitor its stability over time.
NextFlex Puts Digital Technology to Use in Flexible Hybrid Electronics
Digital technology has seemingly endless benefits for NextFlex, the Flexible Hybrid Electronics Institute. Being able to design electronics into flexible materials and substrates allows for compact and lightweight designs, and increased processing power. The flexible designs often lead to increased transmission range, use of lower-cost materials, and a lower cost per unit for manufacturing. The ability to combine flexible hybrid electronics (FHE) with additive manufacturing also has significant implications.
One example of reimagining products to be more sustainable is “one and done” medical applications, which tend to be expensive and discarded after a single use. NextFlex and partners are working on printing electronics for an electrocardiogram (ECG) monitor on biodegradable material – think of a bandage about the size of a credit card. The electronics connect through a mobile device to monitor the heart for up to 24 hours. Someday this could be used by patients at home, as it is reliable, cost-effective, and recyclable.
NextFlex is also working on using a flexible substrate with built-in electronics to do high-mix, high-volume roll-to-roll processing, according to Art Wall, the institute’s Director of Engineering and Fab Operations. In this type of production, you do not need to stop the operation to change out the electronic component. The substrate keeps moving for a more efficient production process.
Advancing Sustainable Advanced Manufacturing
The institutes’ programs that employ new digital and other innovative technologies are helping to meet U.S. climate goals, create jobs for current and next-generation workers, decrease energy use and costs, reduce carbon emissions, and increase America’s global manufacturing competitiveness.
The institutes and their ecosystems share the mission of driving energy efficiency and sustainability in manufacturing. EPIXC (Electrified Processes for Industry without Carbon), the 17th and newest institute in the Manufacturing USA network, was created to address industrial process decarbonization. Its mission is to replace fossil-fuel-based process heating with electric heating. When combined with the transition to renewable-based electricity generation, this becomes a crucial shift in the effort to reduce industrial carbon emissions.
In 2022, the institutes collectively worked with over 2,500 member organizations to collaborate on more than 670 major technology and workforce research and development projects and engaged over 106,000 people in advanced manufacturing training. State, industry, and federal funds contributed $416 million to these activities.
To learn about the many ways in which institutes are helping meet climate goals, visit our Clean Energy Manufacturing page.