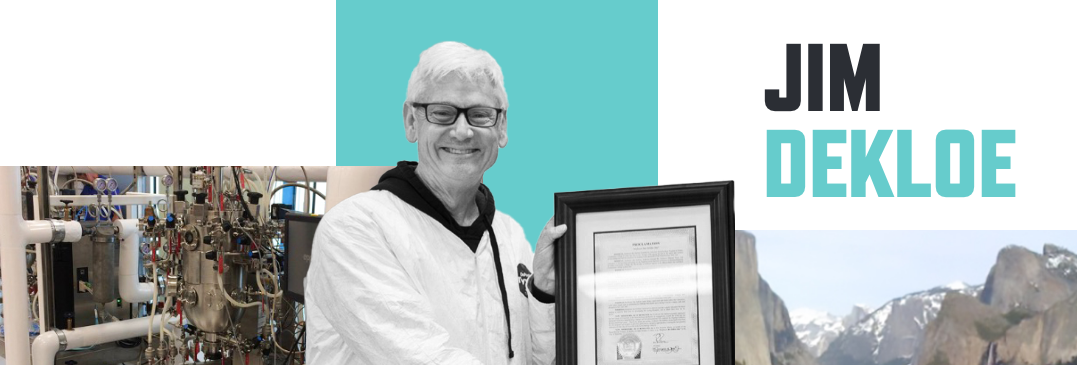
Biotech pioneer, teacher, community advocate
Jim DeKloe is Distinguished Professor of Biological Sciences, Biotechnology, and Biomanufacturing at Solano College in Vacaville, CA. He is a classroom teacher, which entails setting up labs, lectures, making assignments, and grading papers and tests, but Jim is so much more than a teacher; he is a pioneer.
He has helped equip and staff five different laboratories and has written and gained local, regional, and state approval for 10 programs and more than 20 courses. He has given more than 100 invited talks and served as a panelist in more than 20 states. Jim has developed and delivered industry-driven curriculum that incorporates the scientific, technical/engineering, quality, regulatory, and business aspects of biomanufacturing.
However, Jim is most proud of his role in building pathways for great jobs in his community. As the founder of the Industrial Biotechnology program at Solano College, including opening a $34.5 million biotech building on campus, he's helped open the door to biomanufacturing careers now in demand in the areas between San Francisco and Sacramento. He began by developing certificate programs that could be combined with general education classes for an Associate Degree. The program has evolved to now include a four-year degree program.
“Solano County is a population of modest means, the least wealthy county in the nine-county Northern California area. I could see how this might be life-changing for many families.”
Biomanufacturing careers, unlike research careers, do not require an advanced degree. The biomanufacturing field offers excellent wages and promising paths to economic security. “I ask one thing of my students,” he said, “that when they start a new job with a biotech company, they send me a selfie with their new ID badge.”
The High-Growth Curve for Biomanufacturing
Bioindustrial manufacturing uses biological systems – including microbes such as bacteria, yeast, and algae – to create new materials or sustainable alternatives to existing petroleum-based materials. Nearly all manufacturing is based on the use of energy, such as heat, to change the form of something. The biological process on which nearly all biomanufacturing is based is a fairly common one — fermentation.
Fermentation makes use of naturally occurring microorganisms and enzymes to carry out a reaction. It’s how we make bread, kombucha, beer, and wine. Researchers and engineers have identified new ways to use fermentation for manufacturing of almost everything. A small slice of that includes:
- Plastics, paper, and textiles
- Soaps and detergents
- Energy production to generate power from biomass
BioMADE was launched in 2021 to help the U.S. secure global leadership in biomanufacturing, which is projected to be a $4 trillion industry in the U.S. alone by 2030. Jim has been involved in BioMADE since its inception, and he serves on their Education and Workforce Development Committee.
The shared vision of green, sustainable manufacturing prevents climate disruption. It’s on a high-growth curve, which is expected to accelerate as innovations make it more economically viable and more attainable for small manufacturers. “We’re going to need a lot of people in biomanufacturing,” Jim says.

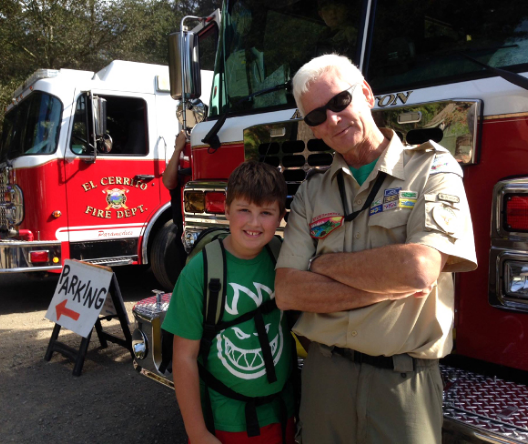
His Journey to the Industrial Side of Biotech
Jim has always been interested in science and earned his undergraduate and Master's degrees and a Ph.D. from UCLA. He thought he was going to be a researcher, but he enjoyed being a teaching assistant and ended up in a tenure-track position at Solano College, where he has worked for the past 33 years, with the exception of 1996, when he took a year off from teaching for a sabbatical at biotech pioneer Genentech Inc. in San Francisco, and a later second sabbatical, with biotech giant, Amgen.
His transition into the manufacturing side of science reveals much about how Jim thinks. For him, the personal investment to make this happen was secondary to the greater cause. “It was the right thing to do, for our students and our community,” he says. “Solano County is a population of modest means, the least wealthy county in the nine-county Northern California area. I could see how this might be life-changing for many families.”
In 1994, before the term biomanufacturing had even been coined or any academic training curriculum had been written, Genentech announced it was building the world’s largest cell manufacturing facility in Solano County. Jim immediately saw the need to train local workforce, and began pitching them on research topics that he could teach. He recounts the CEO interrupting him by saying, “No, no, no. All of that is done by Ph.D.s in South San Francisco. Your students need to know manufacturing. They need to know about the FDA, TQM, GMPs, QA, QC, SOPs, PBRs.” Jim said he wrote the alphabet soup on his arm so he could later look up the terms.
Genentech was looking for expertise to ensure products are consistently produced and controlled according to quality standards and federal guidelines. When Jim acknowledged he knew nothing about that world, the CEO invited him to come to Genentech HQ to learn about manufacturing; and Jim did – for a full year while on a sabbatical.
Jim offers up a sports analogy for how he became immersed in the industrial side of biotech. He says he channeled hockey great Wayne Gretzky, who attributed his success to skating where the puck was going as opposed to chasing it around the rink. If the future of Solano County was going to depend on biotech manufacturing, Jim wanted to be a part of it.
“I ask one thing of my students,” he said, “that when they start a new job with a biotech company, they send me a selfie with their new ID badge.”
The Biotech Script Even Hollywood Couldn’t Write
In 1999, Jim’s 4-year-old son nearly died from a rare infection – few people survive it, and those who do often lose a limb from excessive blood clotting. As the infection set in and his condition quickly worsened, his son was airlifted by helicopter to the Oakland Children’s Hospital.
When Jim and his wife arrived, they were approached by a doctor seeking permission to try an experimental treatment, Tissue Plasminogen Activator (tPA), an enzyme that dissolves blood clots and had been used to treat heart attacks. It had just been approved to treat strokes, but this was believed to be the second time it would be used to treat this type of infection, an “off-label” use in medical terms.
Jim was floored. He had worked on creating tPA during this time at Genentech and in the two years since helped develop programs to train technicians how to manufacture tPA. “There is no drug in the world that I know better than this one,” he recalls saying to the hematologist. He knew the risks, which were significant, but the drug he had helped create might save his son’s life.
The treatment worked, slowly but persistently. After a four-month recovery and rehabilitation at the hospital, and 56 operations, his son returned to full health. The experience has cemented Jim’s resolve. “If you want an advocate for biotechnology, you can find no greater advocate than me,” he says. “Now you know why.”
Bridging the Awareness Gap to Help Grow Biomanufacturing
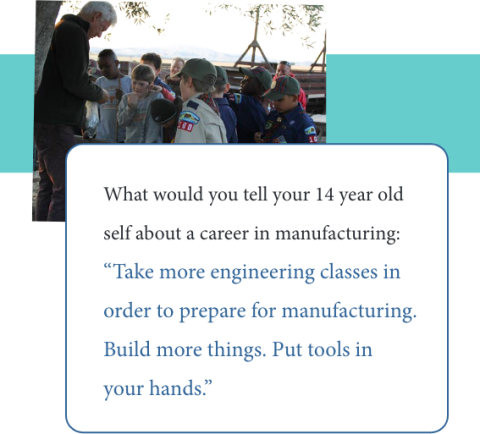
There is almost no area of the U.S. economy that biomanufacturing will not touch, Jim says. He sees biomanufacturing at the heart of reinventing education, bringing economic prosperity via new manufacturing facilities in communities in the central valley of California, Middle America, and Appalachia.
“It’s a classic dilemma – biomanufacturing offers a great career, high salaries, upward mobility and a chance to make a difference,” he says. “Meanwhile, people are unaware of this. We need to bridge that gap and provide them with knowledge and skills.”
Jim’s initial instincts have proven true that funding is more available for “vocational education” than research, but that also is a hurdle. Many of his friends and cohorts see manufacturing as blue-collar as opposed to doing research.
“Biomanufacturing is less intimidating than it sounds,” he says. “One chemistry class will get you a job. Math needs to be contextualized as well. The math required in manufacturing is not calculus. We’re not a trade school, we teach people to think.”